We may earn revenue from the products available on this page and participate in affiliate programs. Learn More ›
Determining the best reloading press is harder than you might think. First off, people reload for different reasons and have different expectations. What suits the casual reloader who wants to craft a couple dozen rounds for a deer rifle each year is worlds apart from the needs of the hardcore handgunner who is trying to get in thousands of trigger pulls in the most economical manner possible. Even in the narrower realm of reloading for precision rifle you have divergent goals — and specialized equipment to match. The way a benchrest shooter reloads is vastly different from how someone like me who shoots ELR and practical field “sniper” style matches makes precision rifle ammo.
So, you can understand why the answer to what’s the best reloading press is: It depends. Part of what also determines the best reloading press for someone is their budget and technical savvy, in addition to their specific ammunition requirements.
Units in the Best Reloading Press Test
- Best For High Volume Precision Rifle: Forster Co-Ax
- Most Versatile: Redding T-7 Turret
- Best High-End Press: Area 419 Zero Press
- Best for High Volume Reloading (tie): Dillon 750XL
- Best for High Volume Reloading (tie): Mark 7 Apex 10
- Best Budget Press: RCBS Summit
- Best Budget Co-Axial Press: Frankford Arsenal M-Press
How I Tested the Best Reloading Presses
For this test I focused on metallic centerfire reloading for handguns and rifles. We’ll cover the gamut of the best reloading presses for shotgunners at another time. (Though if you want to look at a drool-worthy setup for shotgunning, check out this review of the Dillon SL 900.)
To test these presses I, of course, did a bunch of reloading with them. The biggest line of demarcation in this review was between those units I have years (and sometimes decades) of experience with, and those that are new to me.
To keep the test manageable, I limited the number of presses I included. The truth is that there aren’t many reloading presses that flat-out stink. Any press that’s endured for a long time (hello, Rock Chucker) you can purchase with a high degree of confidence.
In terms of my specific protocol, I put each press through a gamut of uses. I loaded centerfire rifle cartridges in different classes based on case length. In the “short” category that included .223 Rem. and 6mm GT, for medium-length cartridges I did 6.5 Creedmoor and .308 Win., and in the longer category I did 6.5 PRC, .300 PRC, and .300 Norma Mag. For handgun ammunition I stuck with loading 9mm.
I resized and decapped brass; primed the brass; seated bullets; and, in some cases, performed extra processes with neck mandrels, expander dies, and the like.
Single-Stage Versus Progressive Reloading Presses
I’ve included both in this roundup, especially since I personally gravitate toward progressive reloading presses for their ability to crank out lots of ammo. That said, if you’re new to the reloading game, a progressive press is not the way to go. Even for experienced reloaders they are complicated and often frustrating.
Among the best advice I got when I started reloading was to keep it simple and just focus on making good ammunition. Don’t worry about volume. Don’t focus on advanced techniques. Simply stick to the basics and craft good ammo. And for that, a single-stage press is your friend. A great resource for someone starting out is this review of the best reloading kits.
Best Reloading Presses: Reviews & Recommendations
Best for High-Volume Precision: Forster Co-Ax
Key Features
- Quick change dies
- Durable construction
- Fast operation
- Includes spent primer catch system
- Uses Forster lock-rings to secure dies
- Ambidextrous operation
- Universal shell holder
- Floating shell holder self-centers brass with the die
Pros
- Fast, smooth, and easy to run
- Precise resizing
- Small footprint
- Reliable
Cons
- High demand means you might need to backorder one
If I tried to tell you how many rounds I’ve loaded on my Forster Co-Ax I’d be guessing — but it is many, many thousands. I’ve run one for nearly two decades and it is my go-to press for resizing precision rifle brass.
At first blush you wouldn’t think this press capable of resizing brass as precisely as it does. There is a fair bit of slop and play in the design. The linkages rattle a bit. The slot that holds the dies induces some wiggle. And in lieu of a traditional shell holder, the press has universal jaws that slide in and pinch the base of the case as it travels up and into the die — yet another moving part.
But all that slop — though I hesitate to use that word because it sounds like a negative — is intentional and helps the press self-align consistently with each stroke of the handle. (In fact, the term Co-Ax refers to the co-axial design of the press and the relationship between how the die is held on one end and how the brass is held on the other.)
When resizing and bumping the shoulders of my 6 GT brass, for instance, about 80 percent of the brass measures the same to the thousandth, while 15 percent might be .001 inches out, plus or minus. The remaining five percent is never more than .002 inches out. That’s great consistency, even for ELR work.
Other single-stage reloading presses are capable of similar consistency, but where the Forster Co-Ax really shines is with its speed.
The shell holder’s pinching jaws grab the rim of the case and center the brass for you meaning you don’t have to guide the case into a narrow slot the way you have to on other presses. Likewise, when you lower the press the jaws let go of the brass making it easy to grab and swap in a new piece. This alone saves many seconds per cycle.
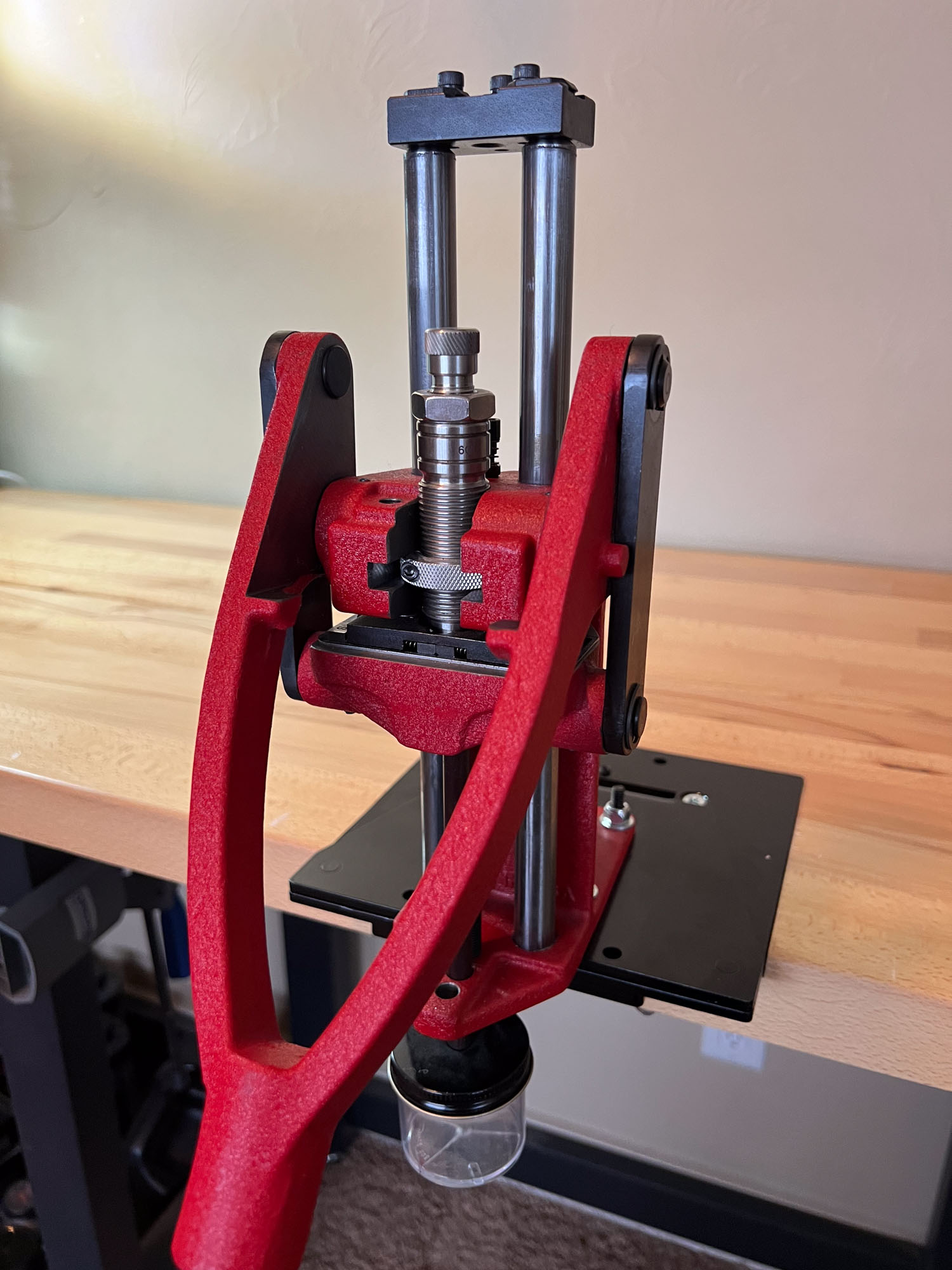
John B. Snow
Like many fans of the Forster, I have a bin of brass that needs resizing on one side of the press and an empty receptacle on the other. Once you get into the flow, the decapping and resizing goes quickly.
The mechanical advantage of the press is remarkable too — and this also contributes to the system’s speed. The stroke to actuate the press is compact but nearly effortless. Even when resizing larger cartridges, like the .300 Win. Mag. or 300 PRC, the Co-Ax doesn’t need to be muscled.
Swapping dies is another area where the Co-Ax is blazing fast. The lock ring on the die — Forster makes their own — slips into the slot on the front of the press and is retained by a simple set screw. With a bit of practice, you switch dies in seconds.
Setting up the dies for correct shoulder bump takes a bit of fiddling and experience to get right. Unlike traditional presses you don’t bottom out the Co-Ax on a shell holder to establish a baseline.
Spent primers drop through a tube into a clear plastic jar. The jar is a bit fragile, so you might end up replacing it at some point, and it is the only element of the press I’d consider weak.
The press also primes brass though it is a little awkward and not a function I personally use.
But overall this fabulous machine is fast, precise, intuitive and easy to run, and a great value as a long-term and reliable investment.
Most Versatile: Redding T-7 Turret
Key Features
- Interchangeable seven-station turret heads
- Rotates between stations quickly
- Cast-iron construction
- More than 3.8 inches of ram travel
- Can be equipped with an automatic priming system
- Shell holders can be rotated to desired orientation
Pros
- Extremely convenient
- Resizes precisely
- Can be run quickly
- Fast toggling between stations
Cons
- Somewhat expensive
This is another press that’s been a mainstay of my reloading room for decades. As for many reloaders, the Redding T-7 was the first premium press I purchased. The beauty of this press is its speed and precision. No other mainstream press is its equal in this regard.
The rotating turret on top lets you mount up to seven dies — enough for two or three different cartridges, or for adding specialized dies to perform specialized operations on your brass.
For instance, I’ll often place a resizing die in one station but remove the expander button from the decapping rod. In the station next to it I’ll place a neck expander die. I’ll resized and decap the brass with one cycle of the press, then rotate the turret to the next die and size the inside of the neck with the next cycle. I can perform both operations in the same time it takes to read this sentence.
(The reason for doing that is because I’m generally not a fan of pulling the expander ball up through the brass — it can pull the shoulder up, messing with your shoulder bump and head space. I’d rather use a dedicated carbide expander mandrel to size the inside of the neck on the downstroke, because it offers better control over neck constriction and yields more consistent results.)
That’s just one example of how you can use the T-7. For reloading handgun ammunition the rotating turret lets you resize, prime, and bell the case neck quickly, and then after adding powder the seating and crimping can be done in a split second.
One thing to know about this press is that with any resizing operation you want solid contact between the shell holder and sizing die. It’s critical that you get a good cam-over when you lower the handle to the bottom of the stroke. That’s because the turret head is designed to tilt ever so slightly to get square to the shell holder.
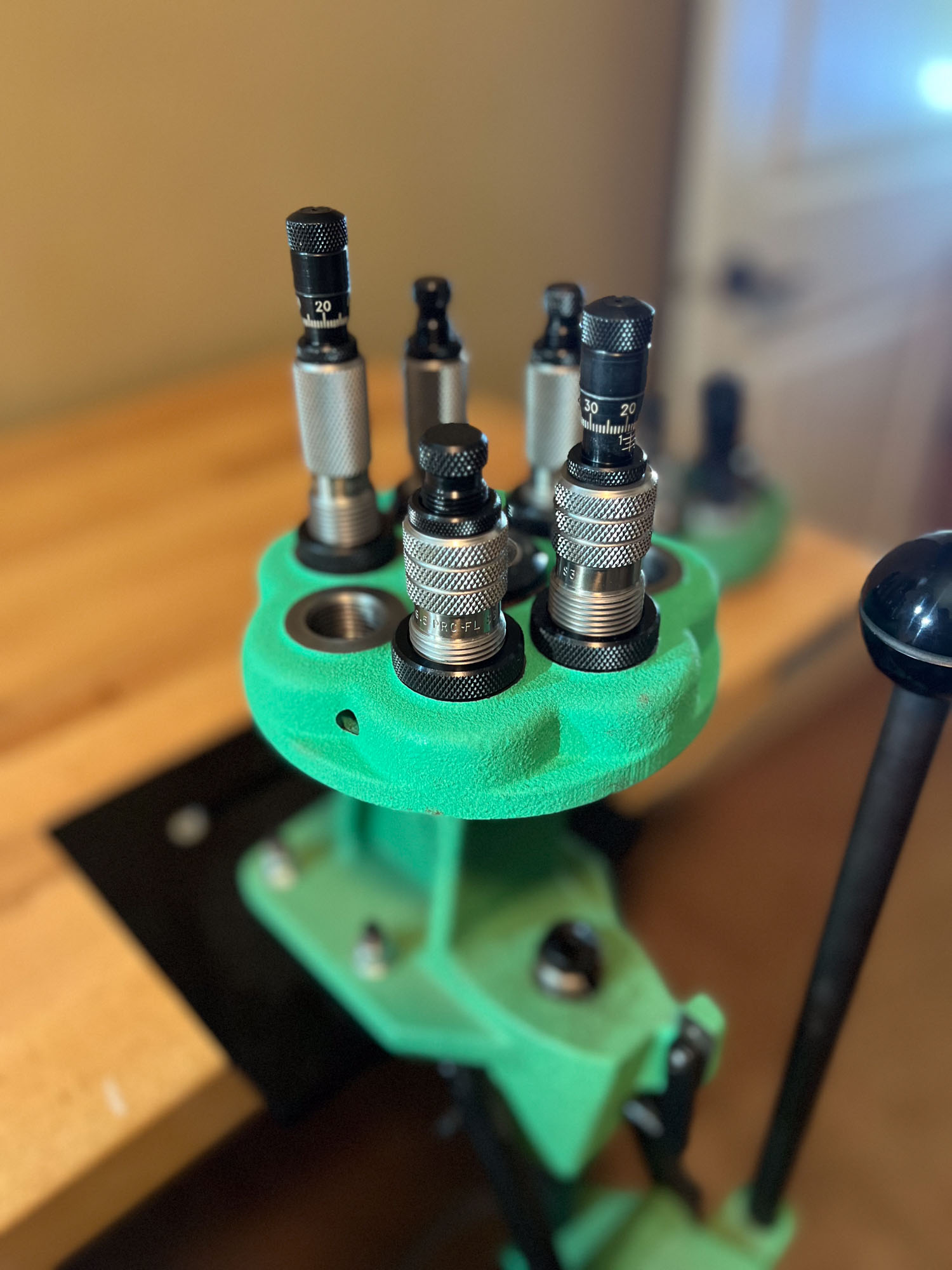
John B. Snow
What this means is that to control your shoulder bump you don’t want to back the sizing die off, as is sometimes recommended. Instead, get the appropriate Competiton Shellholder Set from Redding to precisely set the shoulder bump.
I haven’t used the press’s automatic priming feature in years. I typically prime my brass with either the Primal Right CPS, or the RCBS Automatic Priming Tool that I’ve augmented with Holland’s excellent Perfect Primer Seater adapter unit. Both those allow for fast priming while controlling primer seating depth. That said, the priming system on the Redding T-7 is more than adequate.
New this year is a tool head that can accommodate Redding’s 1-inch dies, which they just released. I’ve only run a few pieces of brass through my 6.5 PRC die but I like the results I’ve seen so far.
The larger-diameter dies provide more support, and are stronger than, traditional 7/8-inch dies and therefore should deliver better results. Yet another reason to consider this press.
Best High-End Reloading Press: Area 419 Zero
Key Features
- Interchangeable turret heads accept 7/8- and 1-1/4-inch dies
- Turret can quickly rotate to go from one die to another
- Turret heads have either eight or nine stations
- Handle adjusts for length and can be attached to either side of press
- Press opening is 4.75 inches with 4.4 inches of ram travel
- Internal contained spent primer catch system
Pros
- Easy to use
- Holds extremely tight tolerances
- Excellent ergonomics
- Great workmanship
Cons
- Expensive
- Resizing is best accomplished with Area 419’s M-Series dies
How excited were precision rifle nerds for the arrival of the Area 419 Zero press? Imagine an arena full of seventh grade girls when Taylor Swift walks on stage and you’ll get the idea.
The Area 419 Zero is a gorgeous piece of work, both to look at and to operate. It exudes quality and precision, so it is little wonder that it produces excellent results.
I’ve been using one since they were introduced, mostly for crafting ELR competition loads. Most of my lever pulls have been with the .300 Norma Mag. and .300 PRC.
Without getting too deep into the weeds, let me say that the Zero Press is the best press I’ve ever used. It is so smooth, gives such great feedback, and is so consistent that I can’t imagine anyone who gets one not being satisfied with the results.
There is one caveat I need to include though. I had issues resizing brass with standard 7/8-inch dies with the press. When I ran the ram, it would tend to bind up and stick. But for bullet seating, running neck mandrels and other processes it was perfect.
Fortunately, Area 419 has a fix for this. It is their M-Series sizing die, which is part of the Zero Press ecosystem, and is a work of art. It is a 1 1/4-inch sizing die that has a micrometer adjustment on top to precisely control shoulder bump. (New Zero Presses ship with the 8-station turret that includes four 1 1/4-inch and four 7/8-inch die locations. You can also get a nine-station turret for just 7/8-inch dies.)
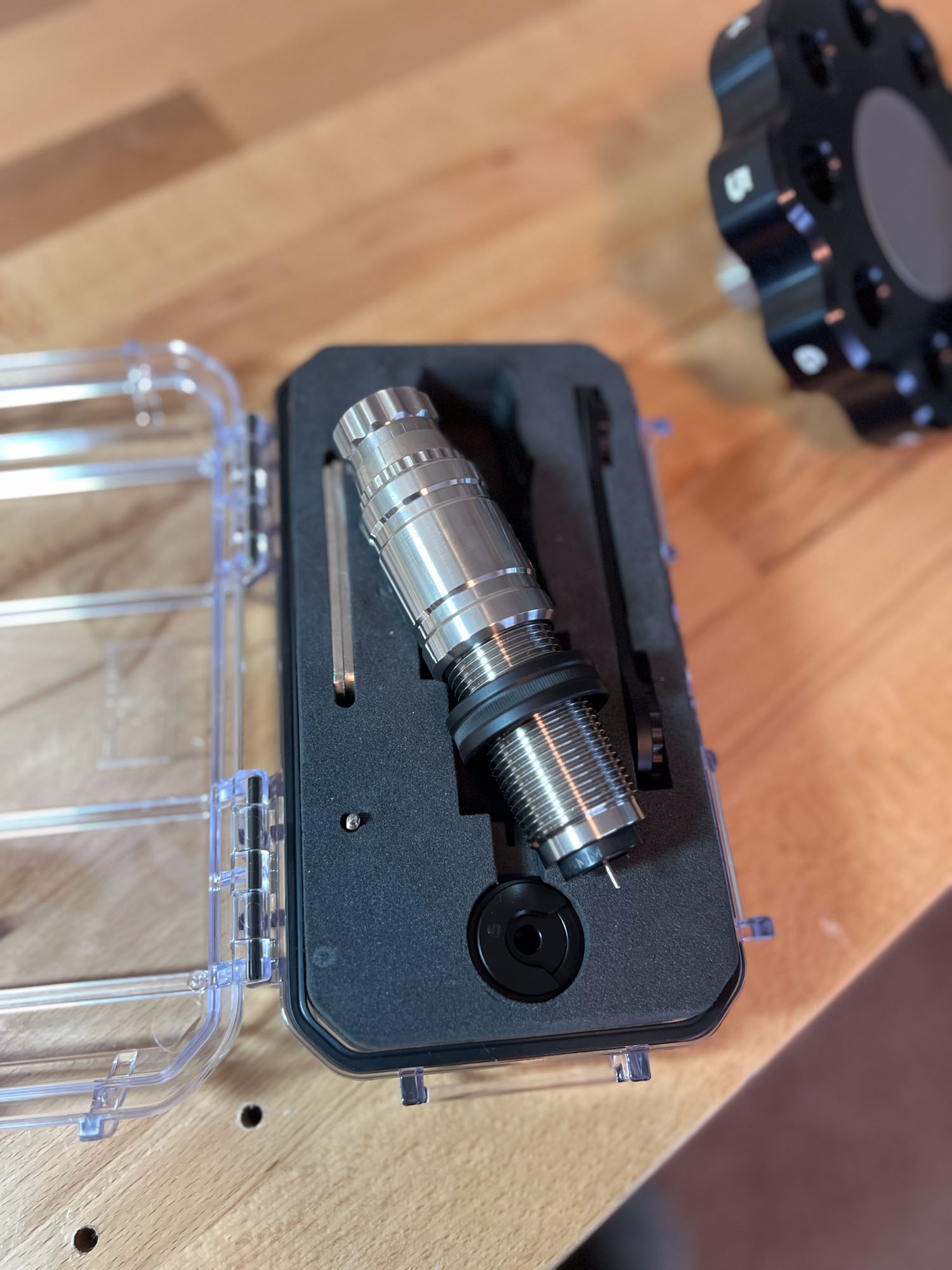
John B. Snow
The first time I tried the M-Series dies I was blown away. They are so easy to use and work so well that it almost feels like cheating. The lineup of M-Series dies is growing, but still somewhat limited. Chances are, however, if the Zero press appeals to you that the cartridges you shoot are on the list.
Here’s the other thing: Like tickets to see T-Swift, buying a Zero press and M-series dies is a spendy proposition. There’s no getting around the fact that it is a significant investment. But if creating precise handloads for your rifle is a priority I doubt you’d regret it.
Best for High Volume Reloading (tie): Dillon XL750
Key Features
- High operating speed
- Five-station tool heads can be swapped
- Can accommodate a wide range of calibers
- Improved primer feeding compared to Dillon XL650
- Easy to upgrade and customize with Dillon accessories
- Many aftermarket accessories available as well
Pros
- Smooth, reliable operation
- Can be adapted to load precision rifle ammunition
- Excellent customer support
Cons
- Complex to set up
Dillon is the foremost producer of progressive presses and has many options in their lineup. The Dillon XL750 is one of their newest presses and replaced their well-known XL650. The machines are similar in many respects, but the XL750 was created in part to address concerns about the XL650’s priming system.
I’ve got both machines and have loaded thousands of rounds of ammunition on my XL650, mostly for precision rifle competitions. Currently, my XL750 is set up for .223 Rem. to make training ammunition for precision rifle.
It does a great job in that capacity. The automatic case feeder, which I highly recommend, is basically bomb proof, and everything else on it works like a charm. Mostly, I’m running new brass through mine, hitting the necks with an expander mandrel to smooth them out. I’m also using the unit to prime the brass, which it does during the forward push on the handle.
You have two routes to follow in terms of dispensing powder. You can either use the included volumetric powder measure or go with a high-speed powder dispenser set up next to the machine, like the RCBS Matchmaster.
The Matchmaster is obviously slower, but more precise, letting you control your powder charges to plus-or-minus a single kernel of powder. The included measure is much faster, not as accurate, but still does a great job helping you craft quality ammunition.
The base price of the XL750 is $739 bucks, but you can trick it out with a lot of add-ons to improve performance. The Casefeeder adds $300 to the unit and is probably the most common (and useful) upgrade. The Powdercheck, for another $100, can be a smart option too, particularly if you’re cranking out handgun ammo.
Best for High Volume Reloading (tie): Mark 7 Apex 10
Key Features
- Ten-stage tool head
- High-quality machining on one-piece frame
- Shell plate indexing, priming system, and volumetric powder measure all able to be fine-tuned
- Can be upgraded to fully automated ammunition production
- Comes with case feeder
- Includes hardware to convert between large and small primers
Pros
- Excellent workmanship and design
- Extremely smooth and ergonomic to operate
- Ten-station tool head provides tons of flexibility
- Outstanding technical support
Cons
- Expensive
- Not ideal for beginners
The Apex 10 is the entry-level model press in the Mark 7 lineup but make no mistake — this is not a press for first-time reloaders. This 10-stage progressive press is a powerful and well-designed machine that can keep up with whatever volume of shooting you engage in, but it requires a fair bit of reloading experience to set up and tune.
The happy place for this press is churning out hundreds (or even thousands) of rounds of pistol ammo an hour, but it can be used (as mine is) to make high quality rifle ammunition too.
I’ve got mine set up to make 6.5 Creedmoor ammo, which I shoot by the pallet each year. I’m making rounds with new and once-fired brass and the Apex 10 does a great job with both.
Operating the machine is a pleasure. The Apex 10 is machined like a Swiss watch. Each pull of the handle is smooth and gives great tactile feedback. It also provides plenty of mechanical advantage so that having the press perform a number of operations at once isn’t fatiguing.
The included case feeder works flawlessly and feeds brass to the first station perfectly each time. From there the brass progress as follows: a sizing and decapping die; neck mandrel; primer station; powder measure; bullet seater; and into the bin on the front of the machine where it lands with a satisfying “plop.” At some point I’d like to add an automatic bullet feeder to make it run even faster.
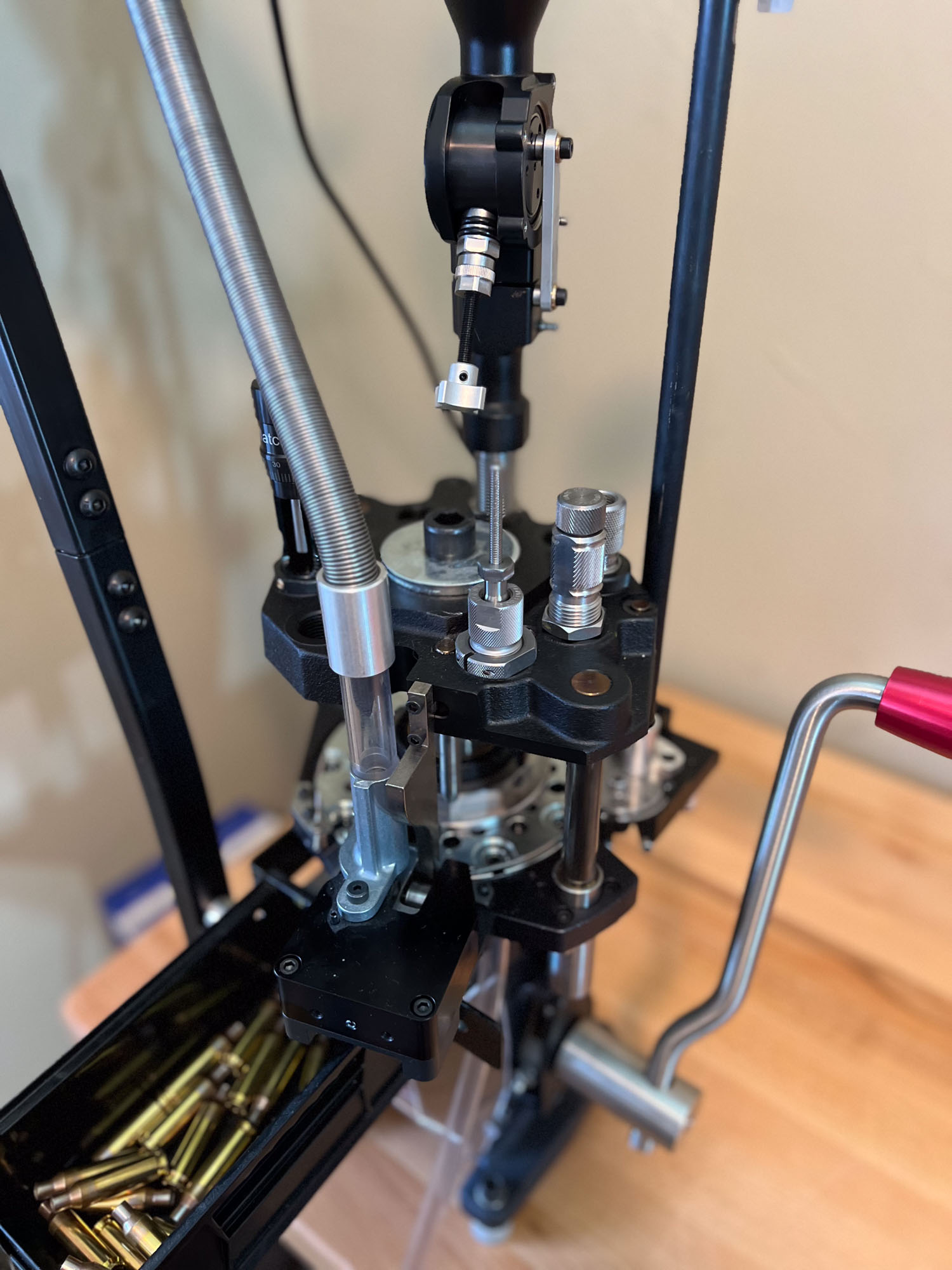
John B. Snow
When getting mine set up I managed to get a primer stuck under the shell plate. I took the machine apart to clear the mishap, and then contacted their technical support because the shell plate wasn’t indexing quite right afterwards.
The tech I spoke with, Jacen Hinkson, was extraordinarily helpful and patient. He not only helped fix the issue, which was minor, but also gave me great insight into the workings of the machine. Know that part of what you pay for when you purchase a complicated press is the company’s technical support.
The $2,500 base price puts the Apex 10 out of reach for many reloaders — and depending on how far you want to go accessorizing it the final figure can be double or triple that amount — but this unit is just a step below a commercial-grade ammunition maker.
For the reloader whose shooting requirements, budget, and desire for quality match up with the Apex 10, it is a terrific choice.
Best Reloading Press On a Budget: RCBS Summit
Key Features
- Oversized 2-inch steel ram
- Cast iron frame and steel linkage
- Compact footprint
- Open design provides ample access
Pros
- Economical
- Easy to use
- Reliable
Cons
- Primer catch bin not very rugged
- Doesn’t prime brass
This basic single-stage press provides a ton of quality for the price. It doesn’t have the bells and whistles associated with progressive- and turret-style presses — but it doesn’t have their shortcomings either.
This is an ideal press for someone getting into reloading. It will let you build your skills and make some damn fine ammo for your rifle or handgun in the process. And the truth is that no matter how experienced and specialized you get with your reloading, you’ll never regret having a good single-stage press on your bench.
The Summit is as simple as it gets. The iron frame has two cutouts for bolts to mount it to your work surface. The long handle can be screwed into either side of the press for ambidextrous operation. And that’s all there is to getting the Summit up and running, other than attaching the primer catch bin with its two fasteners.
The press works by lowering the die onto the brass. The platform the die screws into slides along the 2-inch diameter steel pillar that forms the backbone of the Summit. This leaves the front of the press wide open, making for a convenient work area.
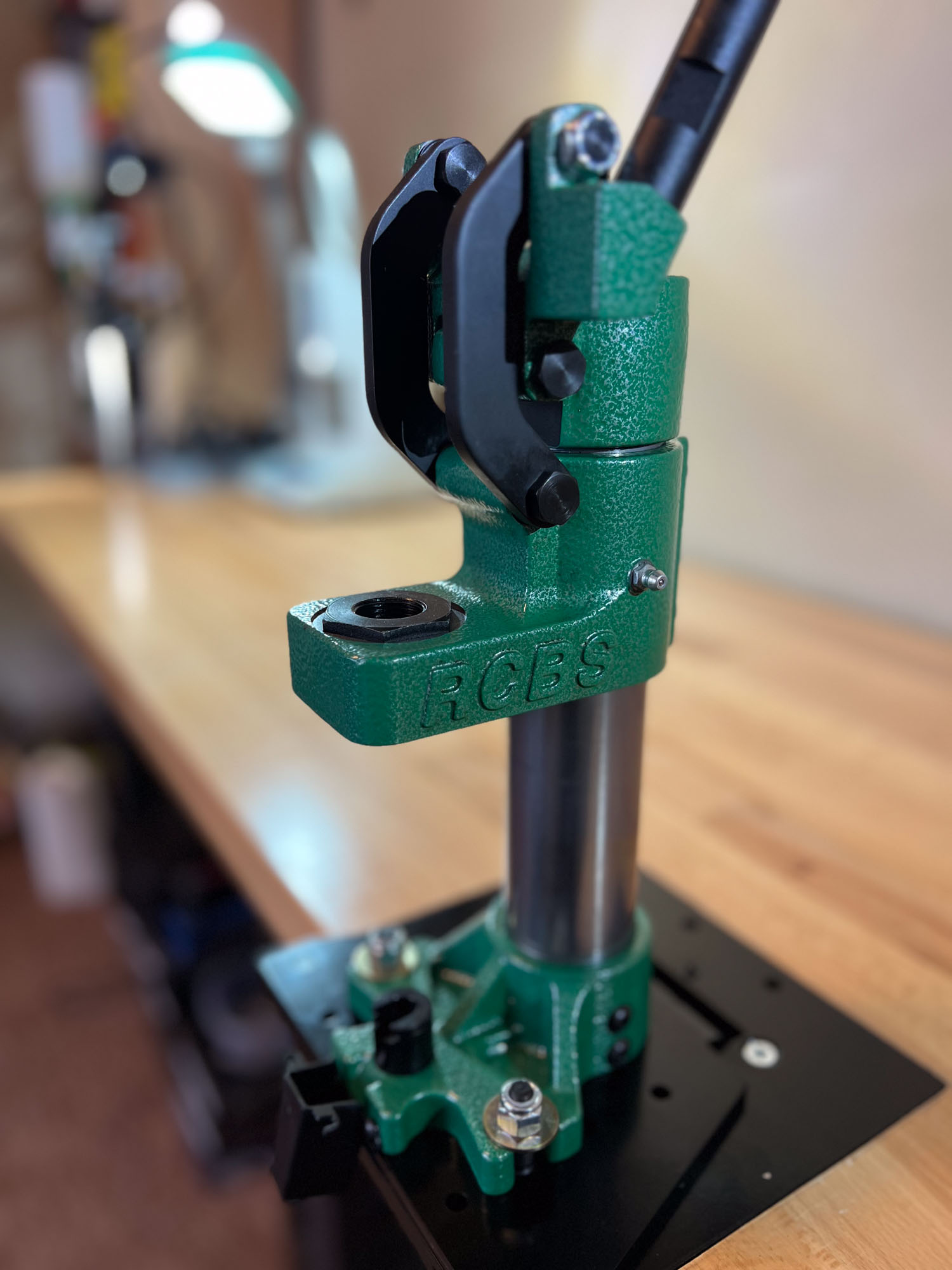
John B. Snow
When fully raised the press has 4.5 inches of clearance so it can accommodate longer cartridges with ease.
The handle that comes with the press is long and provides lots of leverage when resizing. But its length makes it a touch awkward. RCBS sells a shorter handle for $18 that will work better (and be more convenient) when seating bullets, especially in any volume.
The press includes a Zerk fitting (a grease nipple) that allows you to keep it properly lubricated for years of use.
Best Budget Co-Axial Press: Frankford Arsenal M-Press Coaxial
Key Features
- Floating universal shell holder
- Can load everything from small pistol to large magnum cartridges
- Quick change die system
- Includes three floating die blocks
- Doesn’t overhang the bench
- Integrated LED light
- Ambidextrous operation
- Sells for $249
Pros
- Excellent value
- Easy to use
- Smartly designed
Cons
- Doesn’t always deliver the best mechanical advantage
I was incredibly curious about this press before I got it. Given my longstanding and unapologetic affection for the Forster Co-Ax, I wondered whether this relative newcomer (it was introduced about five years ago) could find a place in my heart.
The answer is yes. Like the Forster, the M-Press is a co-axial press, meaning it is designed so that the floating die and the floating shell holder self-align for repeatable results. But there is much that is different between the presses, including some elements where the Frankfort M-Press has the edge.
The headline is that this is a stout, easy-to-use, press that incorporates some clever and useful features. For instance, it has an integral tray that captures spent primers that tucks in out of the way beneath the shell-holder system. And the shell holder system adjusts easily for different size case heads by simply rotating each jaw through the four options (large, small, .223, and .308).
The LED light at the top of the press illuminates the workspace and runs off a micro-USB cable, so you could plug it into an external battery source if a wall socket isn’t available.
The press also comes with three floating die blocks and a convenient storage box to hold them with dies in place. The floating die blocks, which are secured in the frame by a ball-bearing detent, snap into place and out in a flash.
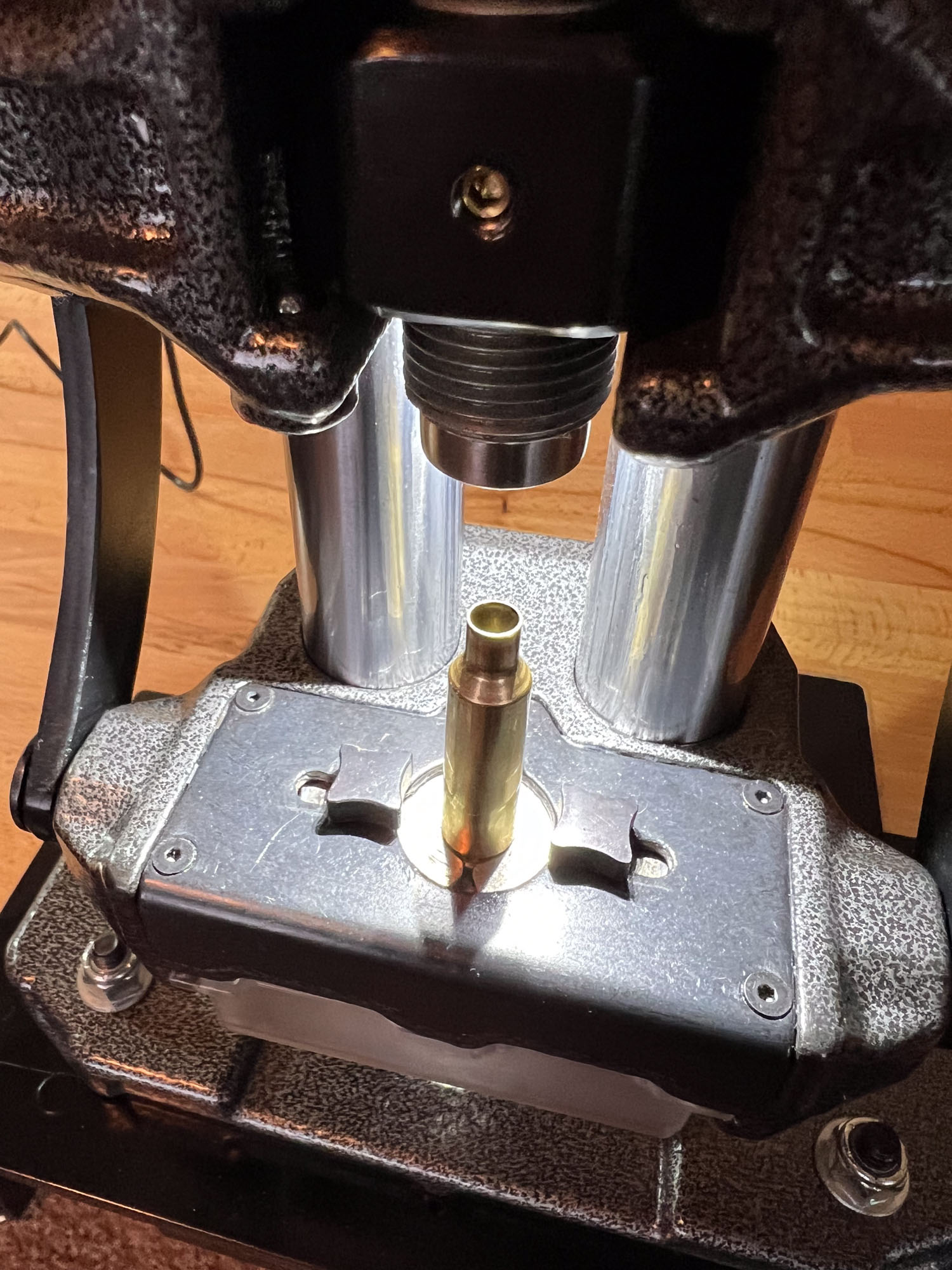
John B. Snow
Another fascinating feature of this press is the ability to change the action of the press from cam-over to a positive stop. You make the change by flipping the linkages, which takes just a couple minutes to do.
I resized a lot of once-fired 6.5 Creed brass in the press. The press delivered good mechanical advantage on the downstroke, but I found when using the ball expander in the full-length sizing die that it caught a bit more than I would expect. I adjusted my technique to “pop” the handle on the upstroke and that dealt with the issue.
It didn’t deliver the same dead-nuts consistency as the Forster, but it was still good. I wouldn’t hesitate to use it to make ammo for my hunting rifle, or practice ammo for my competition rigs. When I switched to the seater die, the press ran perfectly smooth and was wonderfully consistent.
One thing you can’t argue about is the price. At $250 it is a screaming value with a lot of great features.
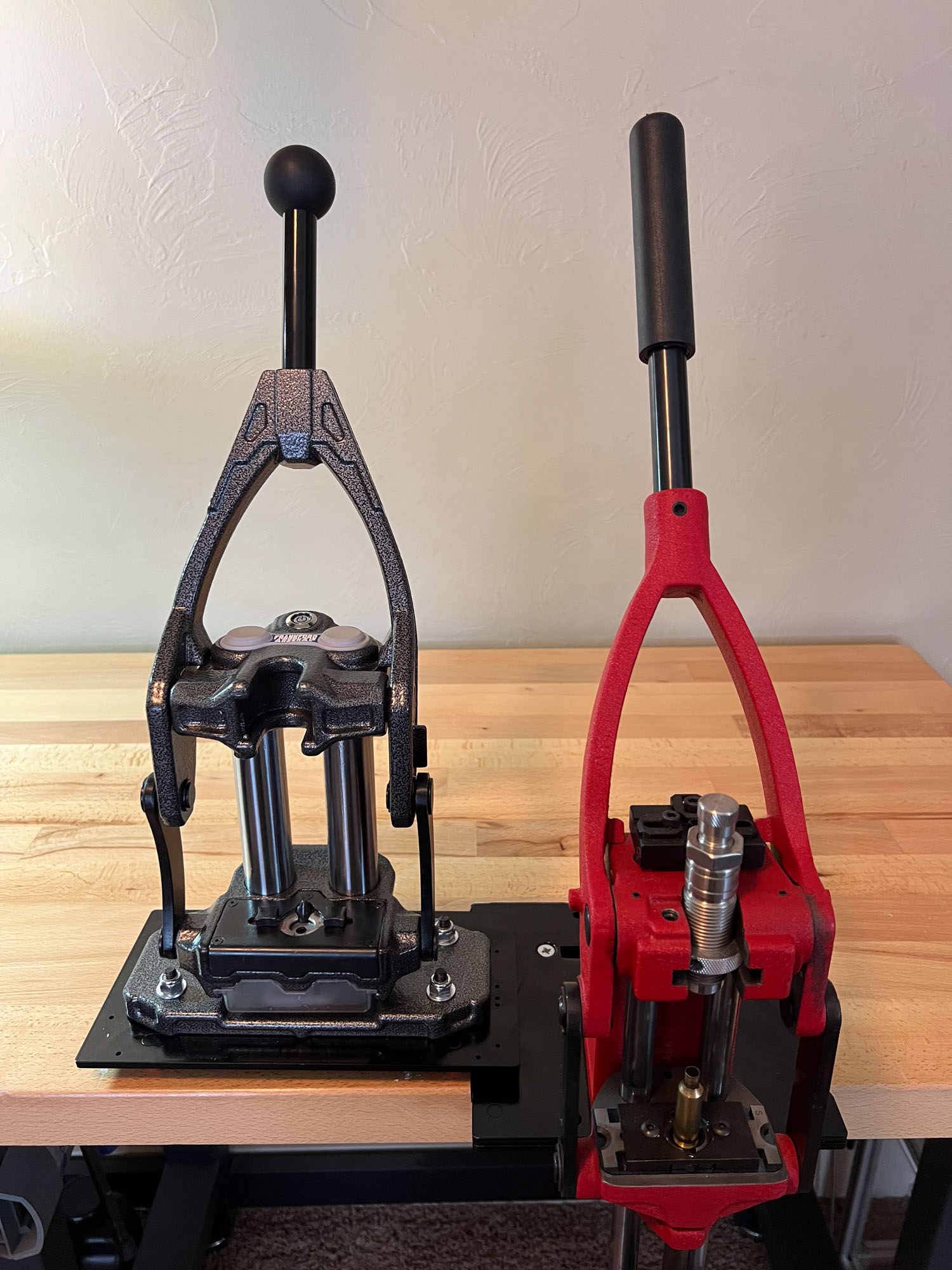
John B. Snow
Notes About Progressive Reloading
There’s a strong line of demarcation between single-stage and progressive reloading that needs to be respected. I touched on this above. Progressive presses generally aren’t a great choice for first timers. That said, if you’re ready to take the plunge don’t let the complexity hold you back. Here are some pointers for when you do.
Take It Slow
When setting up a progressive press don’t hurry. Give yourself plenty of time and don’t necessarily try to do it all at once. I know this might sound overly cautious but trust me — it will save you hassles downstream.
All the bits and pieces of a progressive press need to work in harmony, and if you overlook one small detail during the initial setup it is going to bite you on the tail later. Make sure that when you carve out time to set up the press that you are focused and aren’t contending with other distractions.
Be Methodical
Another thing that can’t be over-emphasized when taking the plunge into the world of progressive presses is to take one step at a time when setting up the dies and stations. So get your sizing/decapping station figured out before adding a bullet seater, primers, or powder drop.
Plan on sacrificing a good amount of brass during this phase as you take measurements and tune each die and station in turn.
Tech Support Is Your Friend
Like most guys I feel that reading instructions is an admission of defeat. When I started fooling with progressive reloaders I needed to check that attitude at the door. They are complex, intricate, and — critically — not intuitive.
So, treat the instructions as though they are a deal you’re striking with the devil. Pay attention to every detail.
Beyond that, take advantage of the company’s technical support services. I know from personal experience that the support staff at Mark 7 and Hornady are excellent in this regard, and I wouldn’t hesitate to lean on them if I’m at all confused.
Be Sensitive
This advice pertains to all reloading but is especially the case with progressive presses. If something doesn’t feel right, stop. Never force the press. Respecting that tactile feedback is critical to avoid making a bad round or possibly breaking something. If the press suddenly feels different, take the time to figure it out.
Maintenance Is Important
Lastly, pay attention to the guidelines concerning lubrication of the press and keep an eye on the tightness of the different bolts and fasteners. You can get away with neglecting many single-stage presses (though you shouldn’t) but you can’t do that with a progressive press.
FAQs
A progressive reloading press is a machine that can perform multiple processes with each pull of the handle. A fully-equipped progressive press can resize and decap your brass, seat a primer, drop a powder charge, and seat a bullet with each cycle. In addition, a progressive press can be set up to swage brass, bell the mouth of a pistol cartridge, crimp a bullet, and use sensors to tell you if something is amiss.
This is an excellent question. And the answer is: sometimes. A lot of today’s factory ammo is wonderfully accurate, and it can be difficult for reloaders to improve on that performance. However, factory ammo can be inconsistent. A particular batch of ammo that shot lights out in the past might not perform as well this time around since ammo makers often substitute components like powders and primers. Reloading allows you to maintain consistency.
Also, if you’re willing to invest in components geared specifically for accuracy and take the time to master them you can certainly improve on even the best factory ammo.
The philosophical answer is your time. Reloading is something you end up devoting many hours to master. Speaking more practically, powder and bullets can be expensive. Powder especially if you load large cartridges that require a lot of propellant. It’s one argument for reloading smaller varmint rounds. Your pound of powder in those pipsqueak cartridges goes further.
In terms of bullets, you get what you pay for. If you’re shooting high-level long-range competition, running premium bullets like Hornady A-Tips or Berger Target Hybrids is going to set you back a bit. Fortunately, there are good bullets for those on a budget that can probably get the job done.
Broadly speaking, the two types of reloading presses are single-stage presses and progressive presses, which we’ve already covered at length. Under these umbrellas are other categories of press designs, like co-axial presses, O-frames, arbor presses, turret presses, automatic indexing progressive presses, and manual progressive presses.
A single-stage reloading press is one that performs a single function with each cycle of the handle. The ram either raises the brass to the die (like the Redding T-7) or lowers the die to the brass (RCBS Summit) depending on its design.
Generally speaking, a single stage press can create loads that are more accurate than a progressive press. That said, progressive presses are regularly used to churn out ammo for long-range rifle competitions. Many top competitors in PRS-style competitions reload on progressives.
Reloading is very safe as long as you take basic precautions. Always wear safety glasses (which is a smart thing to do whenever you use tools of any sort) and keep distractions to a minimum. It is also a smart habit to take good notes. That will keep you on track and help you avoid mishaps.
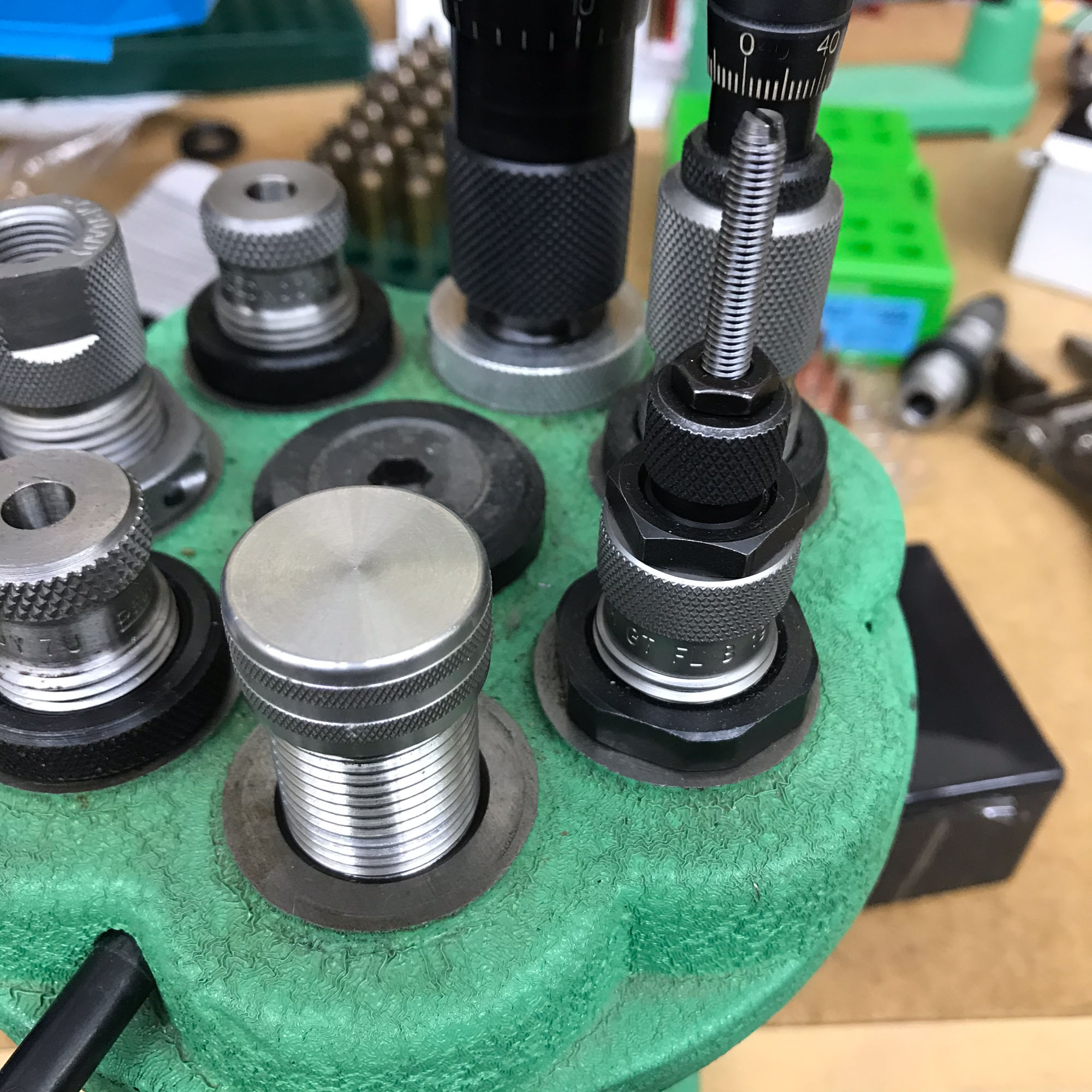
John B. Snow
Final Thoughts on the Best Reloading Presses
While there’s no shortage of good presses out there, the best reloading press for you hinges on your expectations, budget, and expertise.
If you’re new to reloading, stick to the basics. Invest in a good single-stage press and learn how to use it. Or, if you have more money to spend, start with a turret press like the Redding T-7, which is basically a lifetime investment.
If you shoot a high volume of rounds, whether pistol or rifle, then you’re going to want to look at progressive presses, which are designed for that purpose.
Now if you find yourself needing to make a lot of very precise ammo, you’ll likely end up using more than one press to meet your goals while investing in a lot of expensive (but hopefully time-saving) accessories.
In any case, this list of the best reloading presses is a good place to start (or continue) the journey.
- Best For High Volume Precision Rifle: Forster Co-Ax
- Most Versatile: Redding T-7 Turret
- Best High-End Press: Area 419 Zero Press
- Best for High Volume Reloading (tie): Dillon 750XL
- Best for High Volume Reloading (tie): Mark 7 Apex 10
- Best Budget Press: RCBS Summit
- Best Budget Co-Axial Press: Frankford Arsenal M-Press