We may earn revenue from the products available on this page and participate in affiliate programs. Learn More ›
Remember when people used to make stuff with their hands, and folks would gladly pay for handmade products? Well, handmade hunting gear very well could be seeing a renaissance. The downtime from COVID-19 shutdowns and free marketing platforms on social media have given small-time gear makers new opportunities. Plus, there’s a growing demand from consumers for quality, handmade gear.
Whether it’s hobbyists making things for themselves or craftspeople that make a living at it, handmade is in demand.
To explore the undeniable yet undefinable attraction to handmade gear, I talked to a knife maker, a leatherworker, and a bowyer about their businesses and the products they make.
Brent Stubblefield, Join or Die Knives
A piece of steel is a blank canvas, but you can heat it to an orange glow and hit it with precise hammer blows to move the metal into a shape. After a sequence of heating and hitting, you start to have a piece of steel that resembles a tool.
If you take this roughly shaped piece of steel, heat it to its critical temperature and quickly cool it by dunking it in oil, it hardens. It’s getting closer to being more than just a blank canvas, but it still can’t be used for much more than a paperweight. To become a knife, hardened steel needs bevels evenly ground and a handle fitted and shaped. That piece of steel is now a cutting tool that can be a companion to a lifetime of outdoor adventures.
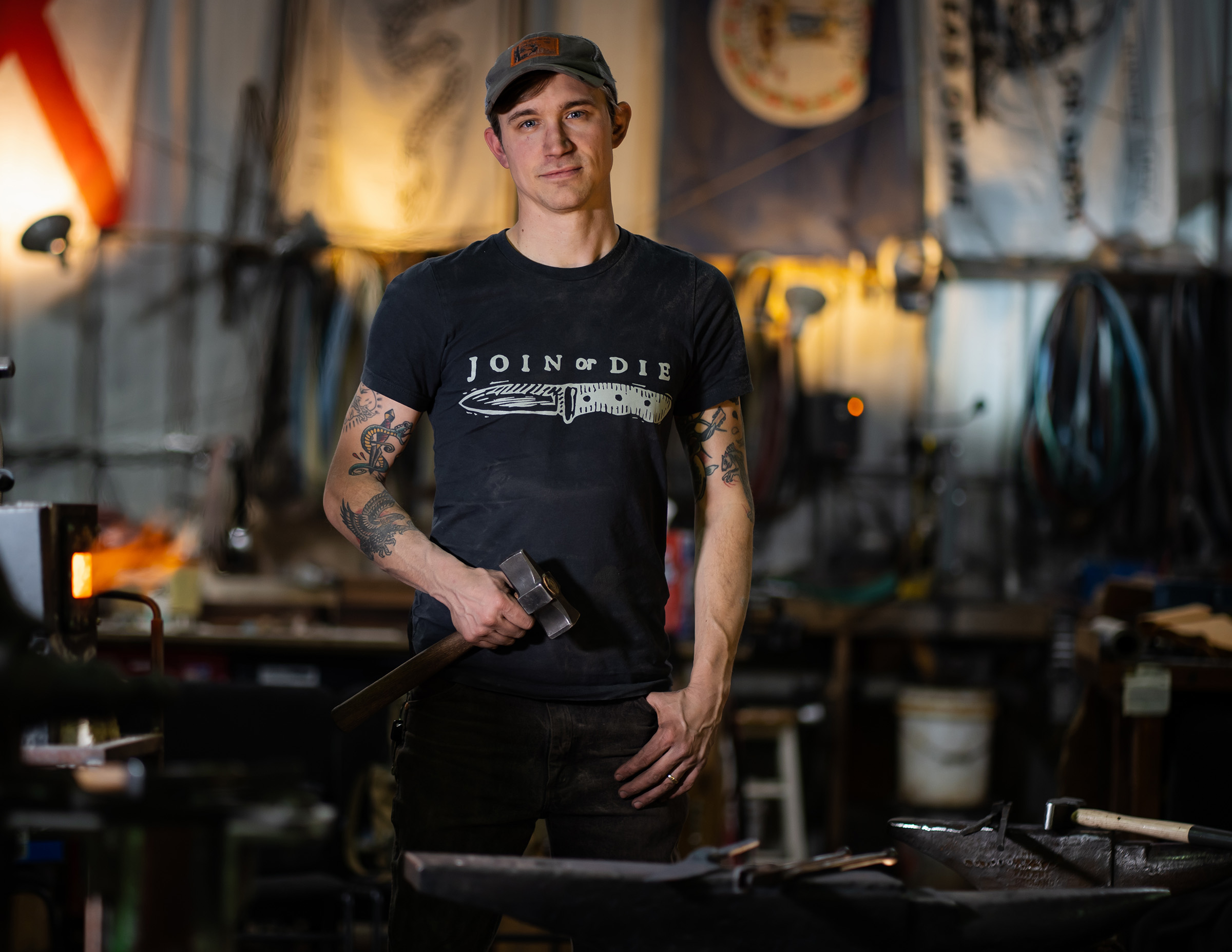
This process of molding raw materials into a useful tool is an alluring process that has recently captivated a wave of new makers. Brent Stubblefield, owner of Join or Die knives in Richmond, Virginia, is a custom knifemaker who also offers classes and a fully equipped knife shop that’s open to the public.
“The knife-making trend has to do with the exposure that it is something that could be done in a home shop,” he said. “Before I got started in knife making, I thought it was something that needed to be done in a facility.”
The growing interest in knife making can be seen in Stubblefield’s introductory classes where anyone can come make a knife over a weekend.
“Sharing what I do with people has been so rewarding,” Stubblefield said. “Especially seeing my students’ pride in their own work and pride in themselves after they’ve come to a class and made a knife.”
The weekend baptism into knife making is a lot like going on your first hunt or fishing trip. You learn new skills, and you can now call yourself a hunter, fisherman, or a maker.
“We’re sharing how to make a knife, but also we’re sharing the identity of being a maker,” Stubblefield said. This identity and the community that comes with it are important to the allure of making handmade products.
“We have people that treat the community shop as a refuge,” Stubblefield said. “That openness and community feeling is so important, and that’s where the name Join or Die comes from, it sounds tough, but it’s about community and not being able to make it alone.”

There isn’t just a resurgence in knife making but also more demand for handmade knives. Why would someone buy a custom knife? “They want that handmade aesthetic, the feeling that you get knowing where something came from and the connection to the person who made it,” Stubblefield said.
Handmade knives typically cost more than production knives. This is because materials are only a small portion that drives cost. The biggest factor is time. Making a knife by hand takes time, but you get a knife that is distinct from those that come from a factory.
“There’s going to be certain features on handmade knives that production knives just won’t have,” Stubblefield said. Those features can be small details like a hand-sanded finish.
When a knife is ground, the grinding belt leaves scratches perpendicular to the knife’s blade. A mark of a handmade knife is hand sanding those scratches away and leaving a finish with sanding lines that go parallel to the knife’s blade. It’s a detail that can’t be mass-produced.
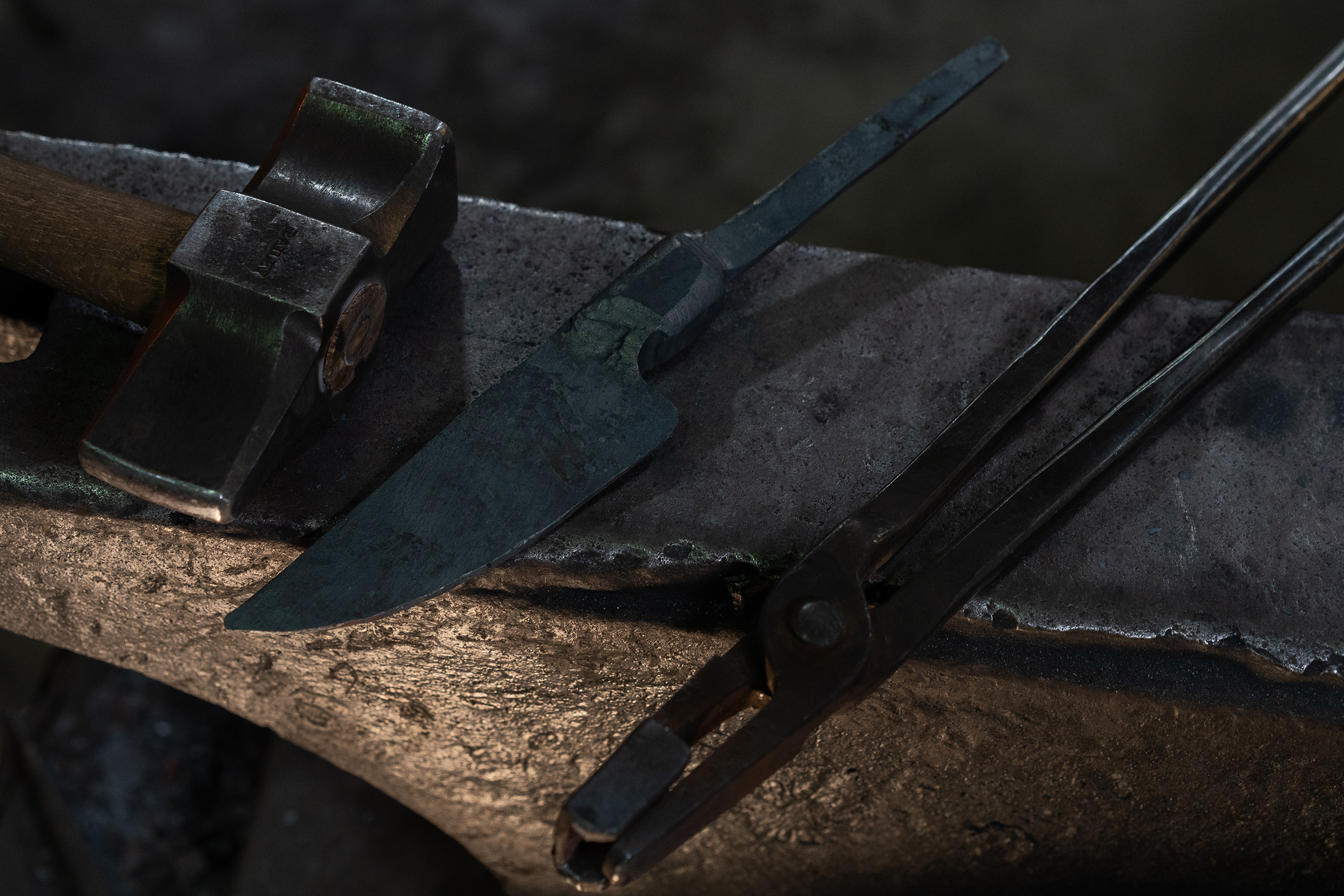
You can still get a knife with handmade features for a price comparable to high-end production knives. Knifemakers utilize time saving tools like lasers or water jet to cut the shape of the knife.
“I want to make knives that someone can buy without blood, sweat and tears,” Stubblefield said. “My $150 knives are my lower price point. Someone might buy one without thinking about it, and someone might save up for months to buy it, but I hope both enjoy the knife equally.”
Of course, there are handmade knives that cost 10 times that price, and they are most often Damascus steel knives. “My favorite knives to make are mosaic Damascus,” Stubblefield said. “There are varying degrees of difficulty with Damascus, and I’m obsessed with producing the most difficult patterns and learning how to create patterns no one has seen before.”
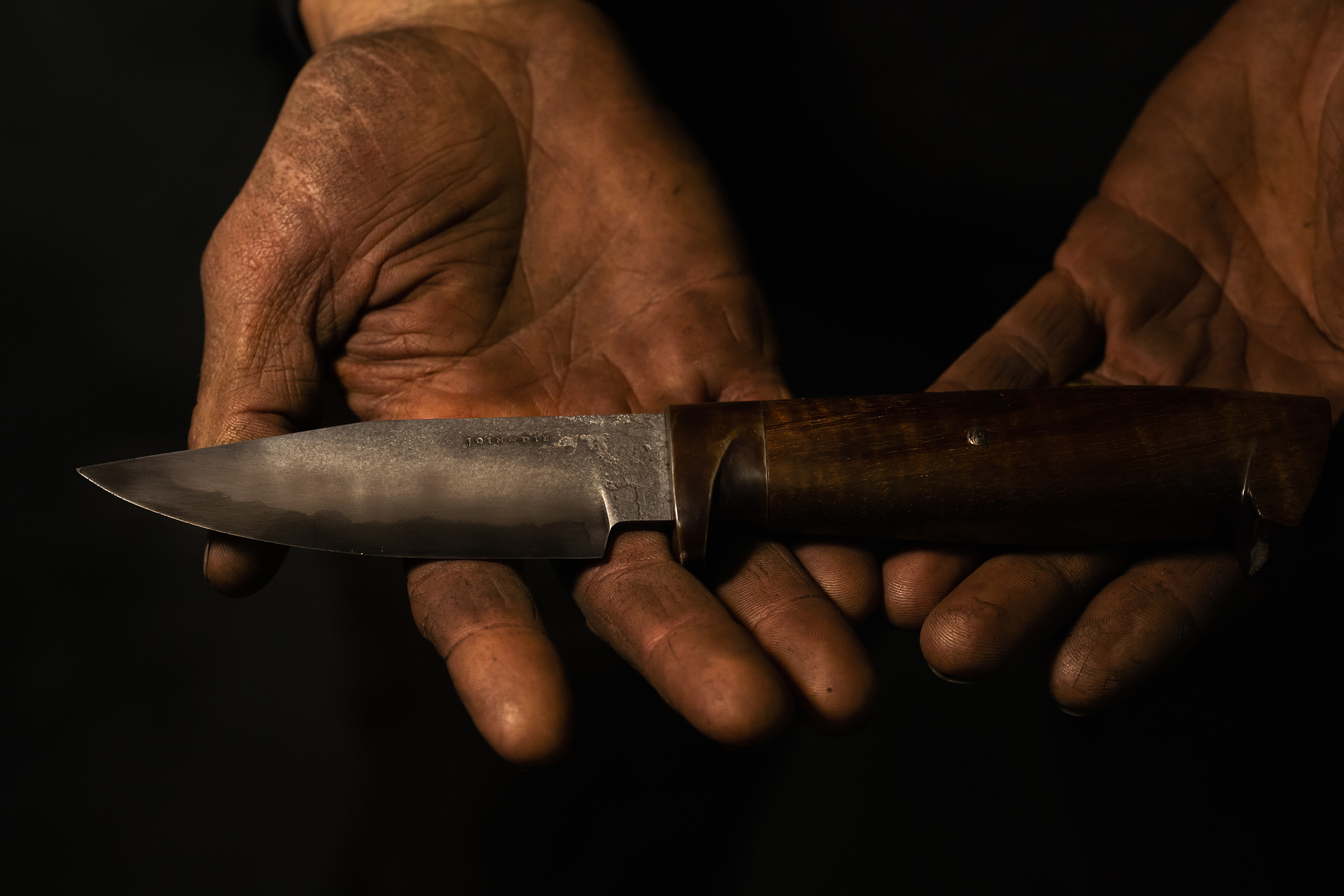
To make a Damascus knife, you must first make the steel. The general concept is to layer two metals with slightly different makeups, so when acid etched, a pattern appears. Mosaic Damascus is the most difficult method of making Damascus, but it creates the most stunning patterns and even pictures in steel. Owning a one-of-a-kind masterpiece like a mosaic Damascus knife is the epitome of embracing the maker renaissance.
Francesca Ritchie, Teton Leather Company
A wallet with a beavertail exterior and bison hide interior isn’t something you’ll find in every store. But it is something you can get from Teton Leather Company in Idaho Falls, Idaho. The company specializes in handmade leather goods made from exotic leather like bison, kangaroo, alligator, moose, stingray, beavertail, and elephant. They do occasionally work with standard cowhide for products like their rifle slings, but even those incorporate beavertail accents that set them apart.
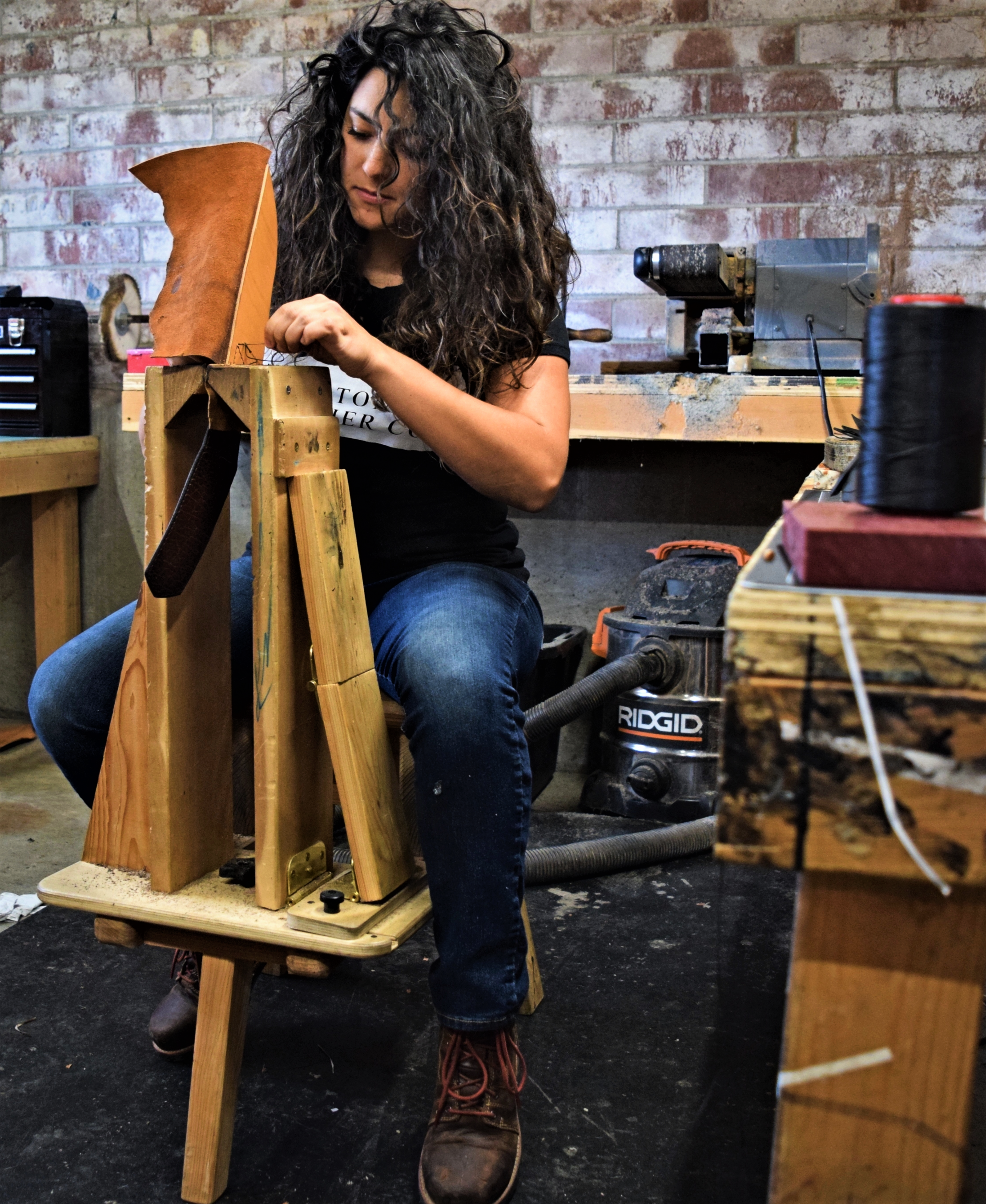
Owners Francesca Ritchie and her husband Zach Ritchie hand make each item. Their products are often custom-made, working with the customer to design a one-of-a-kind project. This combination of unique materials, craftsmanship, and custom design leads to heirloom quality goods. Like the custom knife market, the demand for handmade leather products is booming. “Our business has exploded,” Francesca said. This surge has led to new opportunities like making leather gun cases, rifle slings and whiskey bags in partnership with Griffin and Howe.
You can buy a leather wallet, belt and rifle sling from big box stores, so why are people willing to spend more for one from Teton Leather Company? Materials and craftsmanship.
The materials are the first thing you notice when you look at something made by Francesca Ritchie. The unique textures of beavertail or stingray and the rich tone of bison or moose. “I think working with exotics opens up so many opportunities. They’re all so unique,” Francesca said. “For me, it’s perfect because I can choose from this huge variety of materials.”
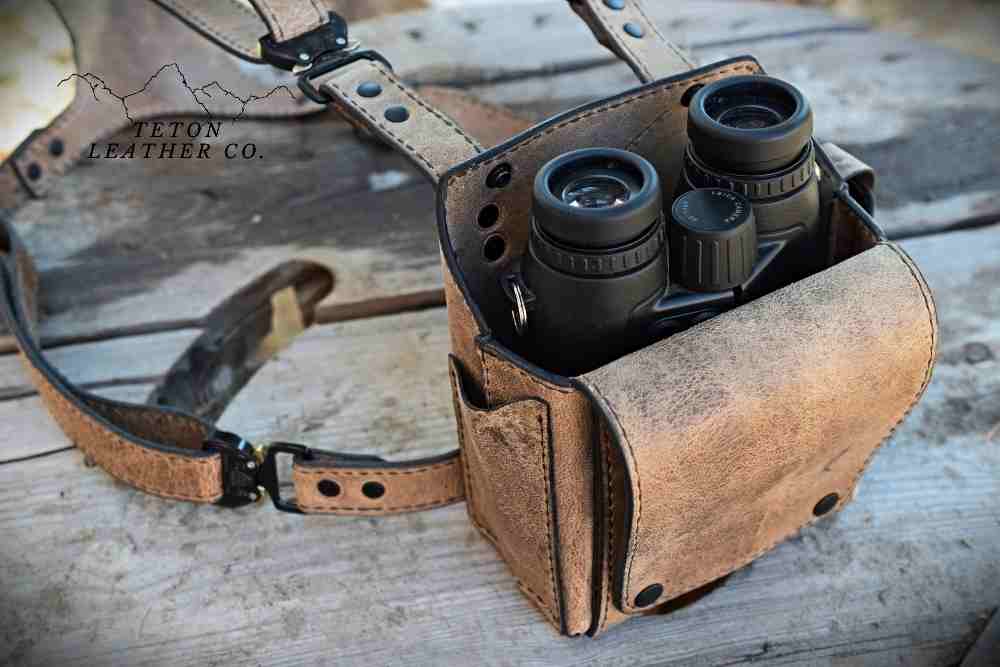
Materials like stingray and beavertail don’t only open creative options. They also create new challenges. “Stingray was used for armor and has a textured feel on one side,” Ritchie said. “The beavertail is an oily leather that requires a completely different cutting technique.”
Despite the challenges that come with these materials, Ritchie is always searching for exciting new leathers to use. “We’re going to go spearfishing for lionfish,” she said. “We’re going to cook them up and use the leather for a special line of goods.”
Ritchie lives for these challenges, and it drives her creativity. “Someone can tell me an idea, and the more challenging it is, it’s almost like a high,” she said. “I love how to make their idea work on leather.”
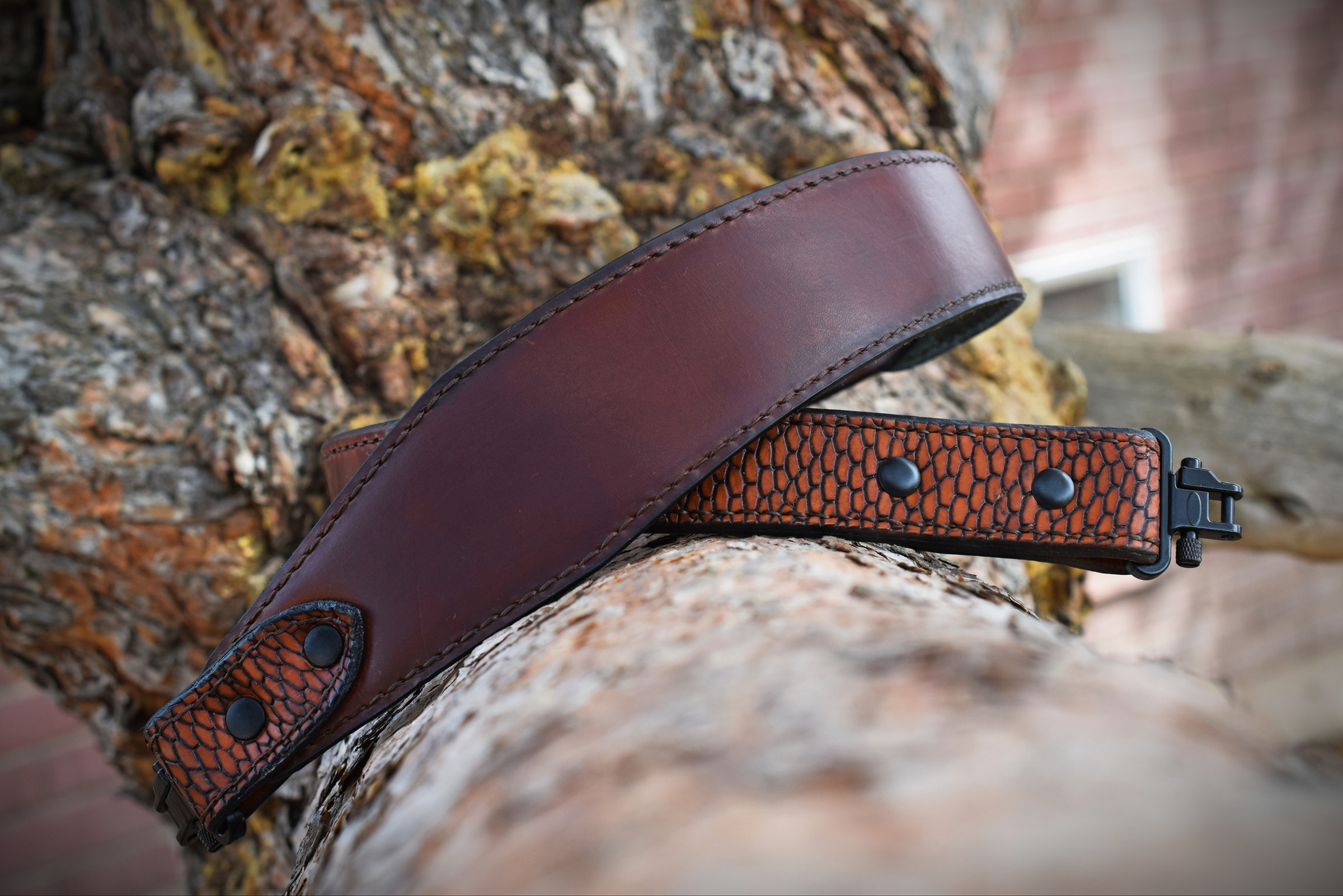
Ritchie’s customers seek her out for her unique selection of materials and superior craftsmanship. Working with unique materials and providing a superior product is what she enjoys most.
“The biggest thing I feed on is the joy my customers get when they receive something that is spectacular,” Ritchie said. “I’d like my legacy to be that I made things that were worth holding onto and they will stand the test of time. They can see the little piece of me that I pour into my work.”
Trent Wengerd, Wengerd Archery
Trent Wengerd of Wengerd Archery in Sandpoint, Idaho makes one of the most sought after recurve bows. The demand for his bows is so great that you can’t get one shipped to you tomorrow, a month from now, or even a year from now. There is currently a two-year waitlist for Wengerd to begin making your bow. But, his customers are happy to wait for their one-of-a-kind bow.
His customers don’t mind the wait because wait times ranging from several months to a year aren’t uncommon for custom traditional bows. “Obviously everyone wants their bow tomorrow if they can,” Wengerd said. “Generally, it’s not a big deal, but I talk to people who aren’t willing to wait that long, and that’s totally understandable.
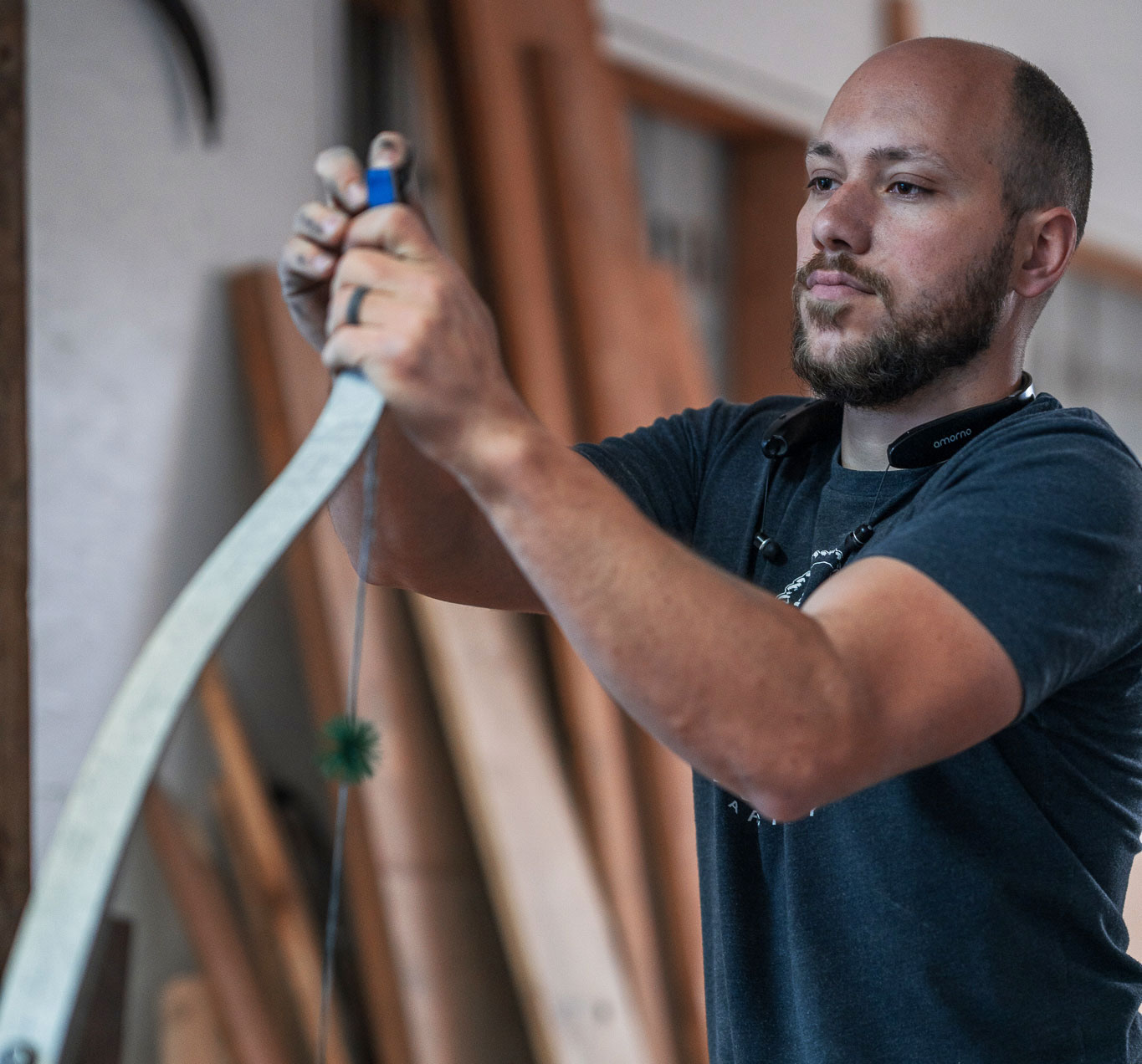
When Wengerd first started his company in 2017, his waitlist was a few months, but it steadily grew, as did many other bow makers’ waitlists. “I definitely think the demand has gone up,” Wengerd said. “I started building bows full-time right when it started blowing up. It seems to have gotten more and more popular.”
Demand is one reason why archers must wait for their bow, the other reason is it takes a long time to make one of these bows. Most bow makers don’t use a CNC machine or other automated machinery to speed up production, and most are one-person operations.
Read Next: So You Want to Hunt With a Traditional Bow?
To build a bow, Wengerd starts by cutting the double-footed flare design from the riser materials which can be made of wood or G10. After the three riser pieces are cut, they’re hand-ground for fit and glued with accent strips between them.
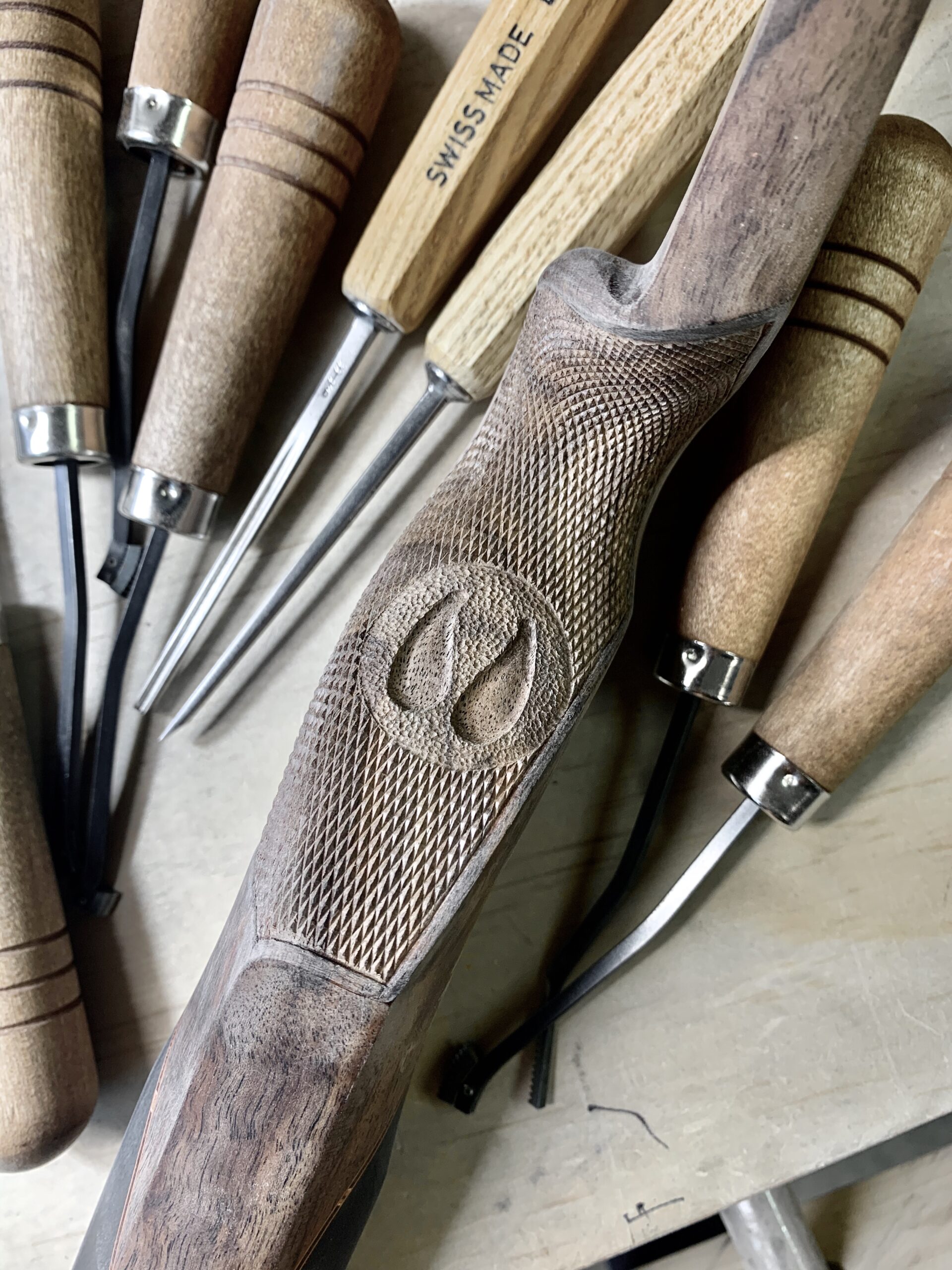
Next, the limbs are made. “I’ll cut the bamboo, carbon, and fiberglass and get them to the proper thickness,” Wengerd said. “That’s how you determine the draw weight, by the thickness of the materials.” The thickness of the “stack” must be precise because just .001 inch can change the draw weight by one pound. Those limb pieces get glued up and cured in a form. The finish work involves cleaning up the excess glue, installing string grooves, overlays, tillering, shaping the grip hand finish and applying an epoxy-based clear coat. The whole process usually takes 15 to 25 hours, but Wengerd has spent several days just adding custom touches like detailed carving.
Wengerd is known for custom touches like detailed relief carving and inlays. “I made a bow for a customer that wanted the entire bow carved. There wasn’t any part of the bow without a carving,” he said. “Bows like that, you don’t forget those because you spend so much time on them.”
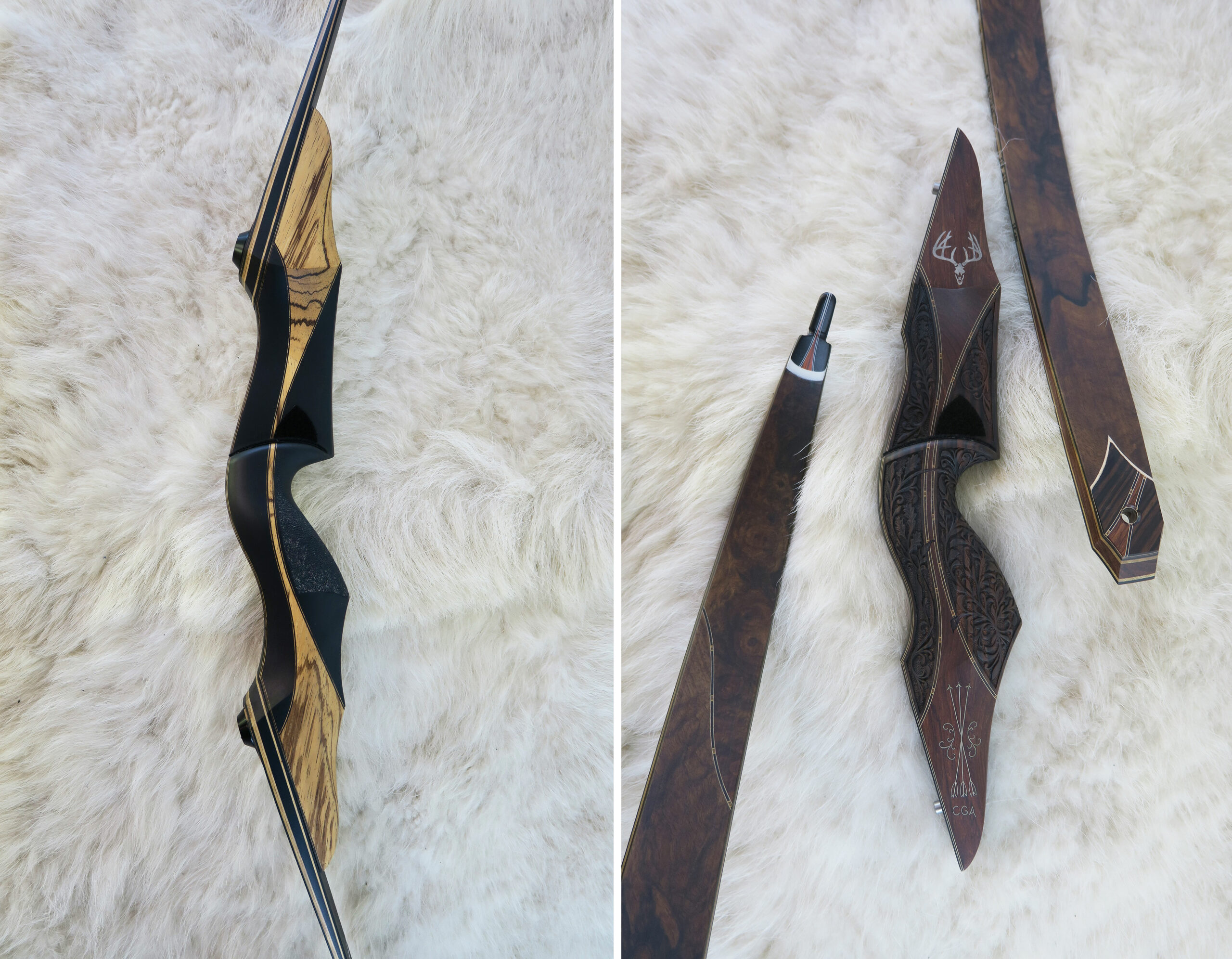
Wengerd’s customers want their custom bows to be custom. “The big thing with custom bows is someone can pick all the little details of the bow,” he said. “There are options for everything from the riser length, limb length, how far the bow is cut past center, exotic woods, custom grips, and even the limb tip design. They really enjoy picking out those different things and being part of the process.”
When we’re part of the process we develop a connection to the bow, the person building it and the memories we’ll make using it. It’s not a bow we’ll buy one year and then upgrade the next. A handmade knife isn’t one that we’ll let rust in a drawer and then throw away. We won’t throw our custom leather gun case in the mud. Handmade gear brings back old-school craftsmanship and the idea that gear is something that should be cared. It’s something that should be passed down from generation to generation.